Dreadfully hot summer weather has brought droughts both literary and literate upon us. The latter is the effect of being a student radio amateur club, where the useful blog post subjects will seasonally migrate to their homesteads or local parks. Therefore we have dived into our archives to bring you tales of a project yet uncompleted.
Norwegian climate tends to bring us many woes, and it often acts as a torture test chamber for the many badly designed outdoor amateur radio devices we purchase. Our complaint this time is with the connectors used on SPID’s BIG-RAS rotator. This is not our first foray with design-oddities of the BIG-RAS, which we have had to weld a better mast bracket for in the past.
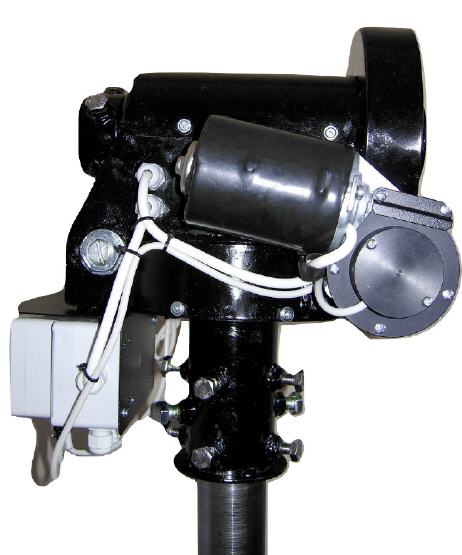
Many a ham will know the 8 pin microphone plug, found on the front panels of nearly every major modern transceiver. Practically no-one would think that this is a suitable connector for outdoor usage. Yet, this is exactly what has been enacted by the SPID coorporation in their outdoor harness for the BIG-RAS rotator.
Our first complaint is that the connector is not out of the box waterproof, and a mess of silicone, heat shrink tubing and self-vulcanizing rubber must be applied if there is to be any hope for the longevity of the product. Apart for the connector not being waterproof, we also discovered that the chassis is a likely candidate for fatigue fractures.
Hard wear on outdoor 8 pin microphone connectors. Fatigure fracture of azimuth connector.
We were lead to discover these facts in painful detail back in January, when we found that the rotor of our parabolic dish had suddenly started to only want to turn in one single direction. The fault was quickly located, a fatigue fracture on the azimuth connector.

Luckily we had another 8 pin microphone connector at the ready to replace the broken subject. We were able to remedy the issue by retouching the solderjoints, and we also reinforced the chassis with a particularly rugged heat shrink tube to prevent the same problem from reoccurring. To our great dismay, this only lasted two weeks, before the connector used for the elevation portion of the rotator also suffered the same fate. Possibly the fault is of our own making, as we did change the position of the electronics box in the aforementioned welding upgrade.
Slapped with corona restrictions and resignation, we haven’t actually gotten around to do anything about this (this is one of the reasons we don’t like to dig too deeply into the shameful closet of deeply procrastinated projects). However, once we get back to our usual bravado, we intend to amend the problem properly by doing a full connector substitution on the rotator. A likely connector candidate is the Ecomate series, or perhaps some better idea will get a hold of us.
Leave a Reply